Table of Contents
Introduction to Concrete and Its Importance
Concrete is a cornerstone of the construction industry, prized for its versatility, durability, and strength. It forms the foundation of modern infrastructure, from homes and commercial buildings to roads, bridges, and dams. Concrete’s popularity stems from its adaptability and crucial role in creating sturdy, long-lasting structures.
What is Concrete Made Of?
It is a composite material primarily made of cement, water, and aggregates like sand, gravel, or crushed stone. The cement acts as a binding agent, and when mixed with water, it undergoes a chemical reaction called hydration. This reaction hardens and strengthens the concrete. The quality and properties of concrete are influenced by the type and proportion of these key components.
Role of Cement in Concrete
Cement is essential in it, doing more than just binding the aggregates. It significantly impacts the overall performance and durability of the final product. Different types of cement, designed for specific applications and environmental conditions, offer unique properties that enhance the functionality and longevity of concrete structures.
Understanding the Hydration Process of Cement
The hydration of cement is crucial for the strength development and setting of it. This process begins when water is added to cement, triggering a series of exothermic chemical reactions. The primary compounds involved are:
- Tricalcium silicate (C3S)
- Dicalcium silicate (C2S)
- Tricalcium aluminate (C3A)
- Tetracalcium aluminoferrite (C4AF)
Each compound reacts with water uniquely, contributing differently to the hydration process and ultimately to the strength of the it.
Compaction Factor Test: Ensuring Workability
The compaction factor test measures concrete’s workability, which is crucial for ensuring the material’s suitability for specific construction applications. This test involves several steps and specific apparatus to determine the degree of compaction achievable under standard conditions.
Procedure for Compaction Factor Test
- Prepare the Sample: Mix the concrete sample according to standard proportions.
- Fill the Upper Hopper: Fill the upper hopper with the concrete sample.
- Allow Concrete to Fall: Open the trap door, allowing concrete to fall into the lower hopper.
- Release into the Mold: Open the trap door of the lower hopper, letting the concrete fall into the mold.
- Weigh and Calculate: Record the weight of partially compacted and fully compacted concrete to calculate the compaction factor.
A higher compaction factor indicates better workability, essential for achieving optimal concrete quality and durability.
Super Plasticizers: Enhancing Concrete Performance
Super plasticizers, also known as high-range water reducers, are chemical admixtures that enhance concrete’s workability and flow properties without compromising strength. They allow for a significant reduction in the water-cement ratio, resulting in stronger, more durable concrete.
Types of Super Plasticizers
- Sulfonated Melamine Formaldehyde (SMF)
- Sulfonated Naphthalene Formaldehyde (SNF)
- Polycarboxylate Ethers (PCE)
Each type offers unique properties that improve the dispersion of cement particles, enhancing hydration and reducing mix viscosity.
Types of Cement: Choosing the Right One
Different types of cement are designed for various applications, each offering distinct characteristics.
Common Types of Cement
- Ordinary Portland Cement (OPC): Versatile and fast-setting, suitable for general construction.
- Portland Pozzolana Cement (PPC): Enhanced durability and resistance to chemical attacks, ideal for marine structures and sewage works.
- Rapid Hardening Cement: Sets quickly and achieves high strength in a short time, perfect for road repairs and emergency projects.
- Sulfate Resisting Cement: Formulated to withstand high sulfate environments, suitable for foundations in aggressive soils.
Ready-Mix Concrete (RMC): Pros and Cons
Ready-Mix Concrete (RMC) is pre-mixed at a batching plant, ensuring uniformity and consistency in quality.
Advantages of RMC
- Consistent Quality: Automated mixing reduces human error.
- Time Efficiency: Eliminates the need for on-site mixing, speeding up project completion.
- Enhanced Workability: Can include specialized additives to meet specific project requirements.
Disadvantages of RMC
- Higher Initial Cost: More expensive than traditional on-site mixing.
- Logistical Challenges: Requires precise timing for transportation and application.
Ensuring Durability in Concrete
Durability determines the longevity and robustness of concrete structures. It’s influenced by environmental conditions, material quality, and mix design.
“1 .Welding Standards: Achieve Excellence with IS Code Guidelines”
“I-Beams: Top 10 Essential Insights, Unleashing the Power in Modern Construction”
“Unlocking Welded Connections and welding: Top 10 Dynamic Techniques for Steel Structures”
Factors Affecting Durability
- Environmental Conditions: Moisture, temperature fluctuations, and chemical attacks.
- Material Quality: High-quality cement, aggregates, and water.
- Mix Design: Optimal water-cement ratio is crucial.
Enhancing Durability
- Proper Curing: Ensures concrete reaches its full strength and durability potential.
- Use of Admixtures: Improves workability and resistance to environmental stresses.
- Supplementary Cementitious Materials (SCMs): Incorporating fly ash, slag, and silica fume enhances durability.
Methods to Check Concrete Durability
Assessing durability is essential for ensuring structural longevity and safety.
Common Testing Methods
- Rebound Hammer Test: Estimates surface hardness and strength.
- Ultrasonic Pulse Velocity (UPV): Measures the velocity of ultrasonic pulses to detect internal flaws.
- Core Sampling: Extracts samples for detailed laboratory analysis.
Introduction to (RCC)
What is RCC?
Reinforced Cement Concrete (RCC) is a vital composite material in modern construction. It combines concrete and steel reinforcement to create strong and durable structures. RCC can handle both compressive and tensile forces, making it indispensable in the construction industry.
Components of RCC
- Concrete: Made from cement, aggregates (sand, gravel, crushed stone), and water. It has high compressive strength.
- Reinforcement: Typically steel bars or meshes, providing the tensile strength that concrete lacks.
Benefits of RCC
- Strength and Stability: Concrete provides compressive strength, while steel reinforcement adds tensile strength.
- Durability: RCC structures can withstand various stresses and strains without losing integrity.
Importance in Construction
RCC is used in a wide range of structures, including residential buildings, commercial complexes, bridges, dams, and highways. Its versatility and cost-effectiveness make it a popular choice.
Historical Development of RCC
Early Innovations
- 1824: Joseph Aspdin invented Portland cement, revolutionizing construction.
- 1850s: François Coignet pioneered steel reinforcement in concrete, improving tensile strength.
Milestones in RCC
- 1884: G. A. Wayss introduced standardized methods for embedding steel in concrete.
- 1903: The Ingalls Building in Cincinnati, Ohio, became the first reinforced concrete skyscraper.
Modern Advances
Recent innovations like fiber-reinforced concrete and high-performance concrete have expanded RCC’s applications, ensuring its continued importance in construction.
Chemical Composition and Properties of Cement
Key Ingredients
- Lime (60-65%): Acts as a binder, forming calcium silicate hydrate (C-S-H) for strength.
- Silica (17-25%): Enhances tensile strength.
- Alumina (3-8%): Influences initial setting time.
- Iron Oxide (0.5-6%): Contributes to hardness and color.
Important Properties
- Setting Time: Initial setting time is about 30 minutes; final setting time is around 10 hours.
- Strength: Compressive strength is tested at 3, 7, and 28 days.
- Durability: Resistance to chemical attacks, weathering, and abrasion is crucial.
Manufacturing Process of Cement
Steps in Cement Production
- Extraction: Limestone, clay, and sand are extracted from quarries.
- Grinding: Raw materials are mixed and ground into a fine powder (raw meal).
- Preheating: Raw meal is heated using hot gases from a kiln.
- Clinker Formation: Raw meal enters the rotary kiln and is heated to around 1450°C, forming clinker.
- Cooling: Clinker is cooled rapidly to stabilize its composition.
- Final Grinding: Clinker is mixed with gypsum and other additives and ground into cement.
Grades of Cement and Their Applications
Common Grades
- Ordinary Portland Cement (OPC)
- OPC 33: For general construction.
- OPC 43: For precast concrete and non-structural elements.
- OPC 53: For high-rise buildings and bridges.
- Portland Pozzolana Cement (PPC)
- Improved workability and resistance to chemical attacks.
- Used in marine structures, hydraulic structures, and mass concreting works.
- Sulfate Resistant Cement (SRC)
- Resists sulfate attacks.
- Ideal for sewage treatment plants and coastal structures.
Standards and Regulations
- Bureau of Indian Standards (BIS)
- American Society for Testing and Materials (ASTM)
- European Norms (EN)
Concrete Mixing Process for Various Applications
Proportioning Materials
Accurate proportioning of cement, aggregates, and water is crucial for the quality of concrete.
Mixing Techniques
- Hand Mixing: Suitable for small-scale jobs.
- Mechanical Mixers: Used for large projects to ensure uniformity.
Mix Categories
- Nominal Mixes: Fixed proportions, used for general construction.
- Design Mixes: Tailored to meet specific strength requirements.
Testing the Strength of Concrete
Common Tests
- Compressive Strength Test: Measures the ability to withstand axial loads.
- Flexural Strength Test: Assesses resistance to bending.
- Tensile Strength Test: Evaluates resistance to tension.
Proportioning Materials for Different Grades of Concrete
Selecting the Right Grade
- M15: For plain concrete work.
- M20 and M25: For structural elements like beams and columns.
- M30 and Above: For heavy-duty structures.
Example Mix Designs
- M20 Concrete: 1 part cement, 1.5 parts sand, 3 parts aggregate, with a 0.5 water-cement ratio.
- M25 Concrete: 1 part cement, 1 part sand, 2 parts aggregate, with a 0.45 water-cement ratio.
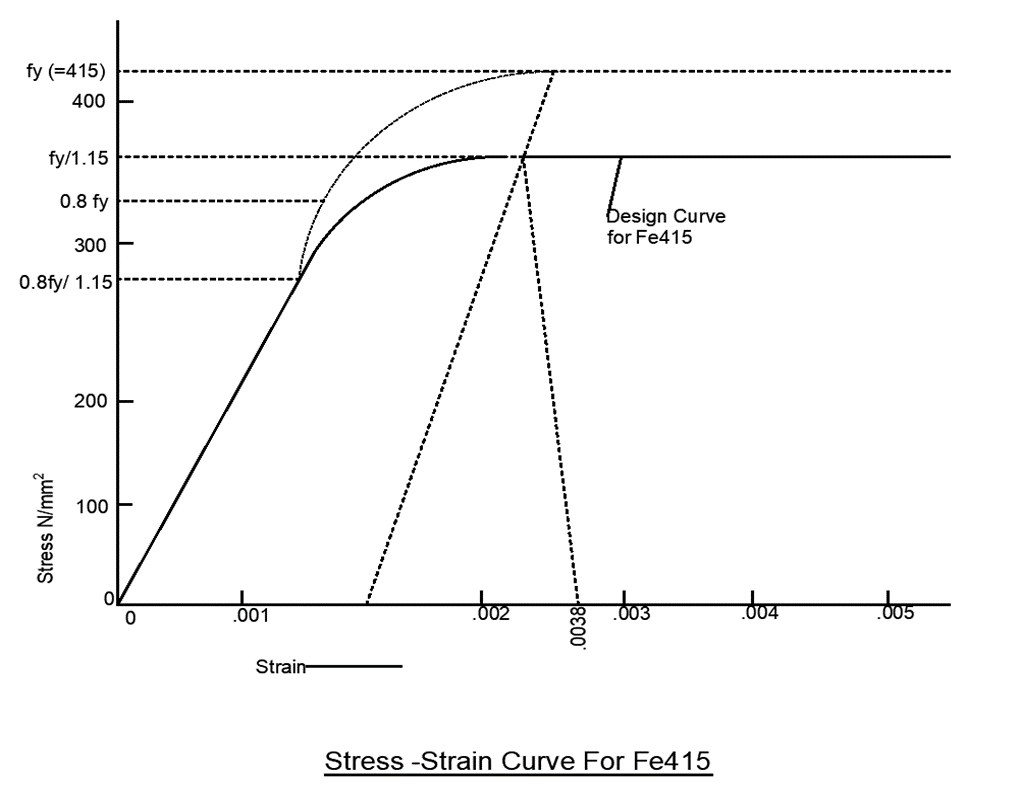
Discover more from
Subscribe to get the latest posts sent to your email.